That's not all. When the burned out rocket stages are blasted off and the next stage is fired up, the satellite is exposed to temporary impulsive vibrations. So how does the satellite survive earthquake-like vibrations, the forces of supersonic shock waves and the pressures of explosive blasts?
French company ARTEC Aerospace developed a vibration and acoustic attenuation technology based on a damping mechanism within the structures, called Smart Passive Damping Device (SPADD®). The principle of the technology is to increase the natural damping of a structure by fixing a light energy-dissipating device to it, without modifying the structure's static behavior.
It could soon be in your car.
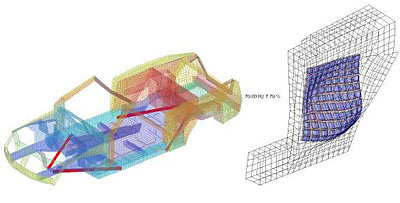
SPADD damping struts for torsion mode damping. Patch treatment at the rear for higher frequencies (the first panel mode with significant damping is shown). Reference: Etienne Balmes: Incorporating damping predictions in the vibroacoustic design process. Credits: SDTOOLS /ARTEC Aerospace
SPADD's damping system is so much superior to traditional dissipation devices that it is considered to be a technological breakthrough in the investigation and research of vibro-acoustics, the area of tackling noise and vibration problems such as those induced by powerful jets or rockets.
The SPADD technology is used on the Ariane launchers and also mounted onboard a number of satellites such as Intelsat, Inmarsat, Integral and MetOp.
Based on this space technology, ARTEC Aerospace has developed tools for optimising the damping in non-space structures. ESA’s Technology Transfer Programme Office (TTPO) supported the transfer of this technology to the car industry through its Technology Transfer Network (TTN).
MST Aerospace, technology broker and leader of TTPO's TTN, then brought ARTEC Aerospace and its SPADD technology together with German car manufacturer Daimler Chrysler AG.

Free and constrained viscoelastic treatments are well established damping techniques, but more efficient solutions can very often be obtained by combining mechanical amplification and constrained layer damping. The figure illustrates such concepts with two SPADDR damping solutions developed by ARTEC Aerospace: SPADD struts (engine mount left) and linear devices (aircraft radar shield right). Reference: Etienne Balmes: Incorporating damping predictions in the vibroacoustic design process. Credits: SDTOOLS /ARTEC Aerospace
The design of convertible vehicles is often based on sibling vehicles of the saloon or coupé line of cars. However, by taking off the top of a self-supporting structure, the convertible’s structure loses stiffness. This leads to torsion vibrations that apart from making for an uncomfortable ride, also make the rear view mirror and the steering wheel shake violently; up to 10 times more than in the saloon version.
At present, the way to correct this is to increase the shell weight of the body but this means that despite the missing top, a convertible weighs around 50 kg more than the saloon version. ARTEC Aerospace demonstrated to Daimler Chrysler that by using SPADD technology on a Mercedes CLK roadster, stiffening elements of 30 to 40 kg mass could be saved.
Successful road tests followed
Since then, DaimlerChrysler and ARTEC Aerospace have been working on implementing the SPADD technology in specific vehicle lines and finding suitable development partners. According to Daimler Chrysler and ARTEC, the results of the cooperation are very promising and have been demonstrated through successful road tests of models with different implementation of the technology.
SPADD has the potential to increase the performance of the structure, for geometrical simplification and for mass and cost savings.
Comments