The optimization and adjustment takes a lot of time and if you are a wealthy elite, the money is less of a worry but for people with musculoskeletal pain the cost may be out of reach.
A new tool replaces pressure-sensitive mats in a confined space with actual workouts or outdoor activities to get a more accurate profile of real-life movement. New insoles created in Switzerland are easy to use, easy to make, and come with integrated sensors and conductors, all using a single extruder. A 3-D printer. For printing, the researchers use various inks developed specifically for this application. As the basis for the insole, the materials scientists use a mixture of silicone and cellulose nanoparticles.
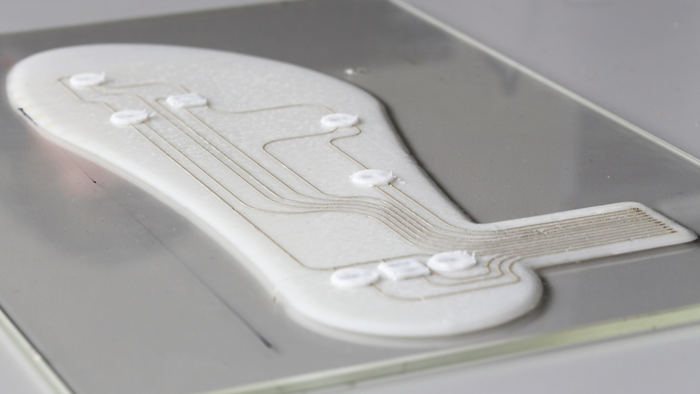
Credit: Marco Binelli / ETH Zurich
Next, they print the conductors on this first layer using a conductive ink containing silver. They then print the sensors on the conductors in individual places using ink that contains carbon black. The sensors aren’t distributed at random: they are placed exactly where the foot sole pressure is greatest. To protect the sensors and conductors, the researchers coat them with another layer of silicone.
An initial difficulty was to achieve good adhesion between the different material layers. The researchers resolved this by treating the surface of the silicone layers with hot plasma. As sensors for measuring normal and shear forces, they use piezoelectric components, which convert mechanical pressure into electrical signals. In addition, the researchers have built an interface into the sole for reading out the generated data.
That means they will be able to see the data in real time.
Comments