While soft, the fabric can be wrapped within a flexible plastic envelope and vacuum-packed, which makes it rigid - 25 times stiffer or harder to bend. This ‘wearable structured fabrics’ could be optimized to harden automatically, or tuned manually when needed. Modern chain mail, anyone? That LARP weekend just got a lot more fun to watch.
The “jamming transition" principle - where solid particles switch from a fluid-like soft state to a solid-like rigid state - is why rice pours easily when loose but becomes really taut inside a vacuum-sealed bag.
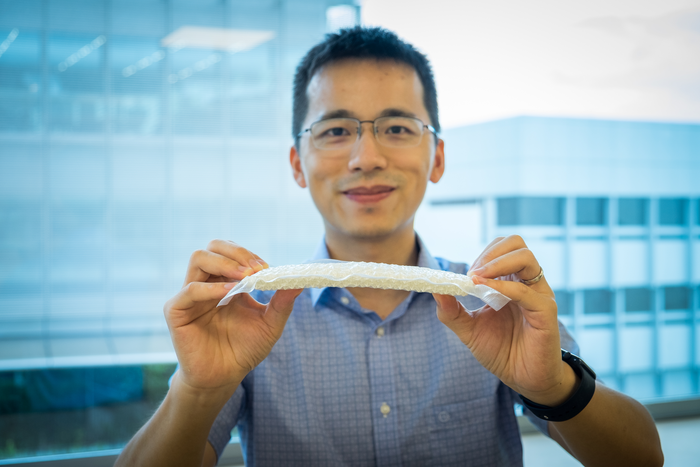
“Inspired by ancient chain mail armor, we used plastic hollow particles that are interlocked to enhance our tunable fabrics’ stiffness," said Nanyang Technological University Professor Wang Yifan. "To further increase the material's stiffness and strength, we are now working on fabrics made from various metals including aluminium, which could be used for larger-scale industrial applications requiring higher load capacity, such as bridges or buildings.” Image: NTU Singapore
The researchers designed structured particles – where each particle is made of hollow frames – in the shape of rings, ovals, squares, cubes, pyramids and different shapes of octahedrons that are then interlocked together. These structures, known as topologically interlocked structures, can then be formed into chain mail fabric that has a low density and yet high tensile stiffness, using state-of-the-art 3D printing technology to print them as a single piece.
They then modelled the number of average contact points per particle and how much each structure will bend in response to the amount of stress applied. The team discovered that by customising the particle shape, there was a trade-off between how much weight the particles will have versus how much the fabric can bend, and how to balance the two factors.
To add a way of controlling the stiffness of the fabric, the team encapsulated the chain mail fabric in a flexible plastic envelope and compacted the fabrics using a vacuum, which applies pressure from the outside. The vacuum pressure increases the packing density of the fabric, causing each particle to have more contact with its neighbours, resulting, for the octahedron-based fabric, in a structure that is 25 times more rigid. When formed into a flat, table-shaped structure and vacuum-locked in place, the fabric could hold a load of 1.5kgs, more than 50 times the fabrics’ own weight.
In another experiment, the team dropped a small steel ball (30 grams, measuring 1.27cm in diameter) onto the chain mail at 3 metres per second. The impact deformed the fabric by up to 26 mm when it was relaxed, but by only 3 mm when it was stiffened, a six times reduction in penetration depth.
To show the possibilities of their fabric concept using different source material, the team 3D-printed the chain mail using aluminium and demonstrated that it has the same flexibility and ‘soft’ performance as nylon when relaxed and yet it could also be ‘jammed’ into structures that are much stiffer compared to nylon due to aluminium’s higher stiffness and strength.
If you are not into being a modern knight, other aapplications may include bullet-proof or stab-proof vests, configurable medical support for the elderly, and protective exoskeletons for high-impact sports or workplaces like construction sites.
Comments